Characterization of Viscoelastic Materials Using Group Shear Wave Speeds - PubMed
Characterization of Viscoelastic Materials Using Group Shear Wave Speeds
Ned C Rouze et al. IEEE Trans Ultrason Ferroelectr Freq Control. 2018 May.
Abstract
Recent investigations of viscoelastic properties of materials have been performed by observing shear wave propagation following localized, impulsive excitations, and Fourier decomposing the shear wave signal to parameterize the frequency-dependent phase velocity using a material model. This paper describes a new method to characterize viscoelastic materials using group shear wave speeds , , and determined from the shear wave displacement, velocity, and acceleration signals, respectively. Materials are modeled using a two-parameter linear attenuation model with phase velocity and dispersion slope at a reference frequency of 200 Hz. Analytically calculated lookup tables are used to determine the two material parameters from pairs of measured group shear wave speeds. Green's function calculations are used to validate the analytic model. Results are reported for measurements in viscoelastic and approximately elastic phantoms and demonstrate good agreement with phase velocities measured using Fourier analysis of the measured shear wave signals. The calculated lookup tables are relatively insensitive to the excitation configuration. While many commercial shear wave elasticity imaging systems report group shear wave speeds as the measures of material stiffness, this paper demonstrates that differences , , and of group speeds are first-order measures of the viscous properties of materials.
Figures
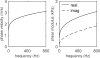
Examples of the phase velocity (left) from (36) and shear modulus (right) from (2) plotted as a function of frequency for the material parameters c200 = 2.5 m/s and c200′=1.75m/s/kHz.
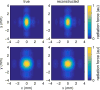
Acoustic radiation force excitation intensities for a C52 transducer with 2.36 MHz excitation frequency. Shown are the normalized intensities calculated using Field-II (left column) and reconstructed intensities using the truncated Fourier series (17) (right column) with −10 ≤ m ≤ 10 for the case of lateral F-number F/1.5 (top row) and F/3.0 (bottom row). The RMS pixel differences between the calculated and reconstructed intensities are less than 0.04% for the F/1.5 case and 0.02% for the F/1.5 case. The reconstructed intensities in the right column have not been normalized, so both the magnitude and shape of the reconstructed forces can be compared with the left column.
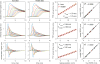
Comparison of true results from Green’s function calculations and results from the analytic model for the case of a material model with c200 = 2.50 m/s and c200′=1.75m/s/kHz m/s/kHz. The top, middle, and bottom rows shows results for displacement, velocity, and acceleration shear wave signals. The first and second columns show true and model shear wave signals at lateral positions 4 ≤ r ≤ 15 mm. The third column shows the TTP arrival times as a function of lateral position, along with the group shear wave speeds estimated from a linear fit of arrival time vs. position. The fourth column shows a comparison of the true and model group speeds for the 14 materials listed in Table 1; the red symbols indicate the material from the three left columns. Diagonal lines indicate equality. Values of R2 are indicated and show excellent agreement between the model and true speeds.
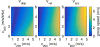
Group shear wave speeds Vdisp, Vvel, and Vacc calculated using a wide range of material parameters c200 and c200′.
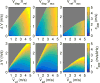
Lookup tables for the phase velocity c200 (top row) and dispersion slope c200′ (bottom row) determined using the Vdisp : Vvel (left), Vdisp : Vacc (center), and Vvel : Vacc (right) pairs of group shear wave speeds. For each pair of speeds, the lookup tables are plotted as a function of the average speed V¯ and difference ΔV, for example, V¯vd=(Vdisp+Vvel)/2 and ΔVvd = Vvel − Vdisp for the Vdisp : Vvel pair of speeds. The lookup table data are plotted as functions of V¯ and ΔV to show the strong correlation between c200 and V¯, and between c200′ and ΔV.
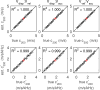
Comparison of the true (x-axes) and estimated (y-axes) values of material parameters c200 (top row) and c200′ (bottom row) for the 14 materials listed in Table 1. Red symbols show the results for the specific case of the material shown in Fig. 3. Estimated values of the parameters were determined using the lookup tables with Vdisp : Vvel (left), Vdisp : Vacc (center), and Vvel : Vacc (right) pairs of group shear wave speeds. Diagonal lines indicate equality. Values of R2 are indicated and show excellent agreement between true and estimated parameters.
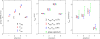
Left, group shear wave speeds Vdisp (black), Vvel (red), and Vacc (blue) from 16 measurements (mean ± standard deviation) in phantoms E2297-A3 (1), E2297-B2 (2), E2297-C2 (3), and E1787-1 (4). The center and right panels show the material parameters c200 and c200′ estimated from the group speeds using lookup tables with Vdisp : Vvel, Vdisp : Vacc, and Vvel : Vacc pairs of group shear wave speeds. These panels also show (green) values of c200 and c200′ determined by nonlinear least squares fitting of (35) to measurements of the frequency-dependent phase velocity shown in Fig. 8.
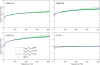
Comparison of phase velocities determined using the group shear wave speed and 2DFT analyses for phantoms E2297-A3, E2297-B2, E2297-C2, and E1787-1. The group shear wave speed results were calculated using (35) and the mean values of material parameters c200 and c200′ shown in Fig. 7 for the Vdisp : Vvel (solid black line), Vdisp : Vacc (dashed red line), and Vvel : Vacc (dotted blue line) lookup tables. Measured values of phase velocity (green, mean ± standard deviation) were determined using the 2DFT analysis of shear wave signals from 16 acquisitions. Material parameters c200 and c200′ obtained using nonlinear, least squares fitting (not shown) of the measured phase velocity are shown in Fig. 7.
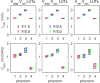
Material parameters c200 (top row) and c200′ (bottom row) estimated from using group shear wave speeds from 16 acquisitions (mean ± standard deviation) for phantoms E2297-A3 (1), E2297-B2 (2), E2297-C2 (3), and E1797-1 (4). Results are determined using lookup tables calculated with F/1.5 (black), F/2.0 (red), F/2.5 (blue), and F/3.0 (green) excitation configurations for the Vdisp : Vvel (left), Vdisp : Vacc (center), and Vvel : Vacc (right) pairs of group shear wave speeds. The results with the F/2.0 excitation configuration are the same as shown in Fig. 7.
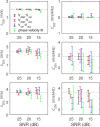
Mean ± standard deviation estimates of c200 (left column) and c200′ (right column) from data sets with 25, 20, and 15 dB white Gaussian noise added to the displacement shear wave signal from Green’s function calculations for three material models with c200 = 1.5 m/s and c200′=0m/s/kHz (top row), c200 = 2.5 m/s and c200′=1.75m/s/kHz (middle row), and c200 = 3.5 m/s and c200′=3.5m/s/kHz (bottom row). The dotted black line shows the true values of c200 and c200′. Results are shown for c200 and c200′ determined using lookup tables with the Vdisp : Vvel (black), Vdisp : Vace (red), and Vvel: Vacc (blue) pairs of group shear wave speeds, and also from fitting of the frequency dependent phase velocity (green).
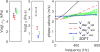
Voigt model analysis of shear wave measurements in the E2297-B2 viscoelastic phantom. The left and center panels show mean ± standard deviation values of stiffness μ0 and vicosity η determined from 16 measurements of group shear wave speeds shown in Fig. 7 (left) and lookup tables determined using the Vdisp : Vvel (black), Vdisp : Vacc (red), and Vvel : Vacc (blue) pairs of group shear wave speeds. The right panel shows the phase velocity calculated from the mean values of μ0 and η using (3), and also the measured phase velocity (mean ± standard deviation, green error bars) from the 2DFT analysis of the propagating shear wave signals. Values of μ0 and η determined from a nonlinear, least squares fit (not shown) of the phase velocity are also shown (green) on the left and center panels.
Similar articles
-
Trutna CA, Rouze NC, Palmeri ML, Nightingale KR. Trutna CA, et al. IEEE Trans Ultrason Ferroelectr Freq Control. 2020 Feb;67(2):286-295. doi: 10.1109/TUFFC.2019.2944126. Epub 2019 Sep 26. IEEE Trans Ultrason Ferroelectr Freq Control. 2020. PMID: 31562083 Free PMC article.
-
Rouze NC, Deng Y, Palmeri ML, Nightingale KR. Rouze NC, et al. Ultrasound Med Biol. 2017 Oct;43(10):2500-2506. doi: 10.1016/j.ultrasmedbio.2017.06.006. Epub 2017 Jul 19. Ultrasound Med Biol. 2017. PMID: 28733030 Free PMC article.
-
Kijanka P, Ambrozinski L, Urban MW. Kijanka P, et al. Ultrasound Med Biol. 2019 Sep;45(9):2540-2553. doi: 10.1016/j.ultrasmedbio.2019.04.016. Epub 2019 Jun 21. Ultrasound Med Biol. 2019. PMID: 31230912 Free PMC article.
-
Error in estimates of tissue material properties from shear wave dispersion ultrasound vibrometry.
Urban MW, Chen S, Greenleaf JF. Urban MW, et al. IEEE Trans Ultrason Ferroelectr Freq Control. 2009 Apr;56(4):748-58. doi: 10.1109/TUFFC.2009.1097. IEEE Trans Ultrason Ferroelectr Freq Control. 2009. PMID: 19406703 Free PMC article.
-
Hossain MM, Gallippi CM. Hossain MM, et al. IEEE Trans Ultrason Ferroelectr Freq Control. 2020 Jun;67(6):1102-1117. doi: 10.1109/TUFFC.2019.2962789. Epub 2019 Dec 30. IEEE Trans Ultrason Ferroelectr Freq Control. 2020. PMID: 31899421 Free PMC article.
Cited by
-
Adjacent tissues modulate shear wave propagation in axially loaded tendons.
Blank JL, Thelen DG. Blank JL, et al. J Mech Behav Biomed Mater. 2023 Nov;147:106138. doi: 10.1016/j.jmbbm.2023.106138. Epub 2023 Sep 28. J Mech Behav Biomed Mater. 2023. PMID: 37782988 Free PMC article.
-
Optimization of the Tracking Beam Sequence in Harmonic Motion Imaging.
Liu Y, Saharkhiz N, Hossain MM, Konofagou EE. Liu Y, et al. IEEE Trans Ultrason Ferroelectr Freq Control. 2024 Jan;71(1):102-116. doi: 10.1109/TUFFC.2023.3329729. Epub 2024 Jan 9. IEEE Trans Ultrason Ferroelectr Freq Control. 2024. PMID: 37917522 Free PMC article.
-
Cai B, Li T, Bo L, Li J, Sullivan R, Sun C, Huberty W, Tian Z. Cai B, et al. Mech Syst Signal Process. 2024 May 15;214:111389. doi: 10.1016/j.ymssp.2024.111389. Epub 2024 Apr 2. Mech Syst Signal Process. 2024. PMID: 38737197
-
Evaluation of Robustness of Local Phase Velocity Imaging in Homogenous Tissue-Mimicking Phantoms.
Wood BG, Kijanka P, Liu HC, Urban MW. Wood BG, et al. Ultrasound Med Biol. 2021 Dec;47(12):3514-3528. doi: 10.1016/j.ultrasmedbio.2021.08.002. Epub 2021 Aug 26. Ultrasound Med Biol. 2021. PMID: 34456084 Free PMC article.
-
Lu G, Li R, Qian X, Chen R, Jiang L, Chen Z, Kirk Shung K, Humayun MS, Zhou Q. Lu G, et al. Phys Med Biol. 2021 Jan 26;66(3):035003. doi: 10.1088/1361-6560/abca04. Phys Med Biol. 2021. PMID: 33181500 Free PMC article.
References
-
- Sarvazyan AP, Rudenko OV, Swanson SD, Fowlkes JB, Emelianov SY. Shear wave elasticity imaging: a new ultrasonic technology of medical diagnostics. Ultrasound Med Biol. 1998;24(9):1419–1435. - PubMed
-
- Nightingale K, McAleavey S, Trahey G. Shearwave generation using acoustic radiation force: in vivo and ex vivo results. Ultrasound Med Biol. 2003;29(12):1715–1723. - PubMed
-
- Bercoff J, Tanter M, Fink M. Supersonic shear imaging: a new technique for soft tissue elasticity mapping. IEEE Trans Ultrason Ferroelectr Freq Control. 2004;51(4):396–409. - PubMed
-
- Chen S, Fatemi M, Greenleaf JF. Quantifying elasticity and viscosity from measurement of shear wave speed dispersion. J Acoust Soc Am. 2004;115(6):2781–2785. - PubMed
-
- Graff KF. Wave Motion in Elastic Solids. Mineola, NY: Dover; 1991. Chap. 5.
Publication types
MeSH terms
LinkOut - more resources
Full Text Sources
Other Literature Sources