Power characteristics with different types of turbochargers for lean boosted hydrogen direct injection engine in NOx-free operation - PubMed
- ️Sun Jan 01 2023
Power characteristics with different types of turbochargers for lean boosted hydrogen direct injection engine in NOx-free operation
Changgi Kim et al. Heliyon. 2023.
Abstract
Lean boosting is a low-temperature combustion technology that can contribute to the expansion of the operation range by reducing the pressure increase rate and the combustion temperature owing to the increase in the intake air amount, even though the amount of heat supplied is the same. By optimizing the boosting device of the direct-injection-type hydrogen engine, it was expected that the operating range could be expanded through the torque increase owing to the increase in the amount of heat supplied according to the increase in the intake air mass, and nitrogen oxides emission was expected to be suppressed owing to lean low-temperature combustion. In the present study, to examine the possible output limit of a hydrogen engine under high-lean boosting conditions by applying a boosting device with a different control method, the performance according to the engine speed was observed under the condition of minimizing nitrogen oxide emission. Owing to the boosting performance by the variable turbocharging device, the output power was improved by 165% compared to that of the naturally aspirated-type combustion at a rotation speed of 5000 rpm.
Keywords: Hydrogen; In-cylinder direct injection; Lean boosting; NOx free; Torque; Turbocharger.
© 2023 The Authors.
Conflict of interest statement
The authors declare no competing interests.
Figures
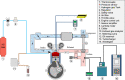
Schematic of experimental setup.
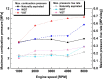
Maximum combustion pressure and maximum pressure rise rate for each boosting condition at various engine speed operation points under wide open throttle (WOT) condition.
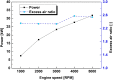
Power output and excess air ratio for naturally aspirated hydrogen engine at various engine speed operation points under WOT condition.
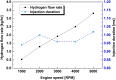
Hydrogen flow rate and the injection duration of the signal applied to the fuel injector for various engine speed operation points under WOT condition of naturally aspirated hydrogen engine.
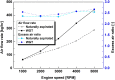
Air flow rate and excess air ratio for each boosting condition at various engine speed operation points with WOT condition.
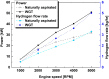
Power output and hydrogen flow rate for each boosting condition at various engine speed operation points under WOT condition.
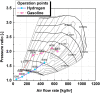
Comparison of the air flow rate and pressure ratio for the hydrogen engine with those of the gasoline engine superimposed on the performance curve of the selected compressor for WGT-type turbocharger under at engine speed operation points under WOT condition.
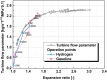
Comparison of the turbine flow parameter and expansion ratio for the hydrogen engine with those of the gasoline engine superimposed on the performance curve of the selected turbine for WGT-type turbocharger at various engine speed operation points under WOT condition.
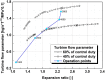
Turbine flow parameter and expansion ratio for the hydrogen engine superimposed on the performance curve of the selected turbine for VGT-type turbocharger at various engine speed operation points under WOT condition.
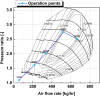
Air flow rate and pressure ratio for the hydrogen engine superimposed on the performance curve of the selected compressor for VGT-type turbocharger at various engine speed operation points under WOT condition.
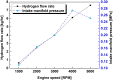
Hydrogen fuel flow rate and the intake manifold pressure at various engine speed operation points under WOT condition of hydrogen engine using VGT-type turbocharger.
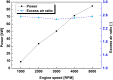
Power output and excess air ratio for turbocharged hydrogen engine using VGT-type turbocharger at various engine speed operation points under WOT condition.
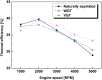
Thermal efficiency for each boosting condition at various engine speed operation points under WOT condition.
Similar articles
-
Zhao Z, Yu X, Huang Y, Sang T, Guo Z, Du Y, Yu L, Li D. Zhao Z, et al. ACS Omega. 2022 Jun 14;7(25):21901-21911. doi: 10.1021/acsomega.2c02154. eCollection 2022 Jun 28. ACS Omega. 2022. PMID: 35785327 Free PMC article.
-
Peng Q, Liu R, Zhou G, Zhao X, Dong S, Zhang Z, Zhang H. Peng Q, et al. ACS Omega. 2023 Jul 27;8(31):27932-27952. doi: 10.1021/acsomega.3c02818. eCollection 2023 Aug 8. ACS Omega. 2023. PMID: 37576650 Free PMC article. Review.
-
Shang W, Yu X, Shi W, Chen Z, Liu H, Yu H, Xing X, Xu T. Shang W, et al. Sensors (Basel). 2022 Feb 6;22(3):1229. doi: 10.3390/s22031229. Sensors (Basel). 2022. PMID: 35161974 Free PMC article.
-
Yilmaz E, Ichiyanagi M, Zheng Q, Guo B, Aratake N, Kodaka M, Shiraishi H, Okada T, Suzuki T. Yilmaz E, et al. Sci Rep. 2023 Jul 19;13(1):11649. doi: 10.1038/s41598-023-38883-3. Sci Rep. 2023. PMID: 37468603 Free PMC article.
-
Aspects of an experimental study of hydrogen use at automotive diesel engine.
Cernat A, Pana C, Negurescu N, Nutu C, Fuiorescu D, Lazaroiu G. Cernat A, et al. Heliyon. 2023 Feb 20;9(3):e13889. doi: 10.1016/j.heliyon.2023.e13889. eCollection 2023 Mar. Heliyon. 2023. PMID: 36895365 Free PMC article. Review.
References
-
- Park C., Kim Y., Choi Y., Lee J., Lim B. The effect of engine speed and cylinder-to-cylinder variations on backfire in a hydrogen-fueled internal combustion engine. Int. J. Hydrogen Energy. 2019;44:22223–22230. doi: 10.1016/j.ijhydene.2019.06.058. - DOI
-
- Park C., Park W., Kim Y., Choi Y., Lim B. Effect of valve timing and excess air ratio on torque in hydrogen-fueled internal combustion engine for UAV. Energies. 2019;12 doi: 10.3390/en12050771. - DOI
-
- Dober G., Hoffmann G., Doradoux L., Meissonnier G. Direct injection systems for hydrogen engines. MTZ Worldw. 2021;82:60–65. doi: 10.1007/s38313-021-0720-5. - DOI
-
- Wimmer A., Wallner T., Ringler J., Gerbig F. 2005. H2-direct Injection – A Highly Promising Combustion Concept. UI - 2005-01-0108. - DOI
-
- Dhyani V., Subramanian K.A. Fundamental characterization of backfire in a hydrogen fuelled spark ignition engine using CFD and experiments. Int. J. Hydrogen Energy. 2019;44:32254–32270. doi: 10.1016/j.ijhydene.2019.10.077. - DOI
LinkOut - more resources
Full Text Sources